สวัสดีครับเพื่อนๆ วันนี้เรามาพูดถึง C ตัวที่ 3 หรือ Cutting กันนะครับ แม้ว่าในธรรมชาติ เพชรเป็นอัญมณีที่มีความสวยงามในตัวเองอยู่แล้ว มีทั้งความใสความแวววาว แต่ทั้งนั้นยังไม่สวยงามมากพอต่อความต้องการของมนุษย์ ที่ต้องการให้เพชรสวยงามมากขึ้นกว่าที่เห็นและมีผู้คนจำนวนมากได้พยายามที่จะทดลอง ”ขัดเงา” เพชรให้มีความวาวมากขึ้น หลังจากนั้นก็เริ่มคิดค้นวิธีการ “เจียระไน” โดยใช้ทักษะที่เคยเจียระไนอัญมณีอื่นมาก่อน เช่น ทับทิม จึงใช้ทักษะนั้นมาพัฒนาให้เป็นการเจียระไนเพชรโดยเริ่มมาตั้งแต่ก่อนคริสต์ศักราช การเจียระไนของเพชรนั้นมีวิวัฒนาการมาอยู่เรื่อยๆเนื่องจากความรู้ทางวิทยาศาสตร์ที่พัฒนาขึ้นมาเรื่อยๆ ทำให้เรารู้จักเพชรมากขึ้น รู้จักกับสมบัติทางแสงของเพชร เข้าใจถึงลักษณะของแสงที่เดินทางผ่านเพชร ทั้งที่เพชรส่วนใหญ่ไม่ได้มีสีที่สวยงามเหมือนอัญมณีต่างๆ แต่เพชรก็มีลักษณะที่สวยงามเฉพาะตัวคือ นั่นคือประกายที่สวยงาม การที่เพชรมีประกายที่สวยงามต่างจากอัญมณีอื่นๆเป็นเพราะเพชรมีค่าดัชนีหักเของแสงสูงกว่าอัญมณีอื่นๆ เพชรมีการกระจายแสงที่ดี เพชรมีความแข็งที่สูงมากจึงทำให้สามารถขัดเงาเพชรได้อย่างเต็มที่ ผิวของเพชรจึงมีความวาวมากกว่าอัญมณีอื่นๆ เมื่อเราเข้าใจสมบัติทางกายภาพและทางแสงของเพชร และได้นำความรู้นั้นมาปรับปรุงวิธีการเจียระไน เพื่อให้เพชรสามารถสะท้อนเอาแสงที่สวยงามออกมาให้ได้มากที่สุด รวมถึงความสามารถ และความชำนาญในการเจียระไน เพื่อตกแต่งเหลี่ยมแต่ละเหลี่ยมให้ได้ตามผู้เชี่ยวชาญได้คำนวณเอาไว้ ถึงตอนนี้เพชรก็จะสามารถเปิดเผยความงามออกมาได้มากที่สุด ทีนี้เรามารู้จักกับเพชรเหลี่ยมเกสรหรือที่มีชื่อภาษาอังกฤษว่า RBC (Round Brilliant Cut) เป็นเพชรที่จะพบเห็นได้มากที่สุดในตลาดเพราะเป็นเหลี่ยมมาตรฐานครับ ลองดูรูปนะครับแล้วจะรู้ว่าแต่ละส่วนของเพชรทรงนี้มีชื่อเรียกว่าอะไรกันบ้าง
จากรูปนะครับเพชรเหลี่ยมเกสร จะแบ่งเป็น 2 ส่วนคือส่วนบนที่เรียกว่า Crown และส่วนล่างที่เรียกว่า Pavilionซึ่งแต่ละส่วนมีส่วนประกอบดังนี้ครับ
คำถามต่อมาที่เพื่อนๆจะถามก็คือแล้วเราจะรู้ได้ยังไงว่าเพชรเม็ดนี้เจียระไน สวยไม่สวยยังไง ถ้าจะให้ผมพูดคงต้องร่ายกันยาวมากๆ และการประเมินว่าเพชรเม็ดนี้สวยไม่สวย ต้องใช้ประสบการณ์พอสมควรครับ เอาเป็นว่าผมมีตาราง สัดส่วนของการเจียระไนที่ดีมาให้เพื่อนๆดูครับ ถ้ายังไงลองเอาตารางนี้ไปเทียบกับ ใบ Certificate ของเพชรที่ออกให้โดยแต่ละสถาบันดูนะครับ เพราะในใบ Certificate จะมีระบุสัดส่วนต่างๆเหมือนดั่งตารางครับ ถ้าเวลาซื้อเพชรจะสามารถขอดูได้จากเจ้าของร้านเลย *Certificateเพชรที่ออกจากสถาบันต่างๆนั้นส่วนใหญ่นิยมออกให้กับเพชรที่มีขนาดตั้งแต่ 0.5ct ขึ้นไปนะครับเพราะว่าต้องมีค่าใช้จ่ายในการตรวจสอบและออกใบรับรองของสถาบันต่างๆ แต่ถ้าเป็นเม็ดเล็กๆเพื่อนๆอาจจะลองถามทางเจ้าของดูว่าเค้ามี Certificate รึเปล่า บางร้านก็จะมี Certificate ที่ทางร้านออกให้เอง ซึ่งก็น่าเชื่อถือได้ในระดับหนึ่งครับ ใครจะกล้าเอาชื่อเสียงร้านมาเสี่ยงครับถ้าไม่แน่ใจว่าเป็นของจริง จริงมั้ยล่ะครับ การเจียระไน ตอนที่ 2 (Cutting)สวัสดีครับเพื่อนๆ ตามสัญญานะครับ วันนี้ผมจะพาไปรู้จักกับเหลี่ยมเพชรแบบต่างๆนะครับ สำหรับการเจียระไนเพชร เหลี่ยมหลักๆก็มีไม่เยอะหรอกครับ ที่เพื่อนๆควรรู้เอาไว้ก็ตามข้างล่างเลยนะครับ
ทั้งหมดนี้ก็เป็นเหลี่ยมเพชรที่เพื่อนๆน่าจะได้พบเจอตามร้าน Jewelery ทั่วไปนะครับ แต่จริงๆแล้วเหลี่ยมของเพชรนั้นยังมีอีกหลายแบบขึ้นอยู่กับคนเจียระไน ว่าเข้าจะเจียระไนแบบไหนด้วย สำหรับวันนี้ ผมขอตัวก่อนนะครับ โชคดี สุขภาพแข็งแรงกันถ้วนหน้าครับ……โอ เครดิต พลอย Wobito สวยมั้ยคะ เค้าทำยังไงเรามาดูกัน คลิกที่ View Discovery Channel Video ด้านล่างนี้เลยค่ะ THE GEM CUTTING PROCESSThere are a number of good machines available for cutting precious stones - a process called faceting. Although the machines may look complicated, they consist primarily of a grinding plate called a lap and a set of protractors that help the faceter hold the stone accurately against the lap. The faceter controls the actual faceting process during the grinding and polishing processes on each face of the stone. A faceted gem begins with the selection of faceting rough, which is chosen for color, clarity, type of stone, shape, and perhaps some other qualities as well. Cutting designs are often selected to suit the piece of rough. But, in this case I selected the rough to support a specific design. For the gem documented on this page, I selected a unique piece of rutilated quartz. I obtained this shaped and tumbled piece at a rock show and bought it because it displayed a needle surrounded by a large clear area (center of stone). The plan for this gem is to cut it carefully around the needle, centering the needle down the middle of the finished piece. I started by grinding away much of the unwanted rough to prepare the stone for attaching to the machine. The left view is looking down the needle, the right view shows the needle from the side. Note a tiny stray needle next to the left end of the one we're going to use. Gems in progress are attached to the machine via a small peg called a dop. The rough stone is attached to the dop by means of hot wax glue. The most challenging part of creating this novel gem design is orienting the gem rough on the dop. Orientation is critical so that the needle will wind up in the center of the finished stone where the pavilion faces will reflect it like a kaleidoscope. I begin by grinding a flat spot to mate with the flat end of the dop. Then, after the rough is glued to the dop, I grind some temporary faces around the circumference (girdle) of the stone and cut temporary pavilion faces at about 35 degrees. This creates a point in the very center of the pavilion so I can see how good my initial orientation was. I make adjustments by warming the dop wax and gently moving the stone. After each adjustment, I recut both the girdle and the temporary pavilion faces. Then, I examine the needle's appearance both at the point of the temporary culet and in the girdle faces. Rotating the dop between my fingers helps me to see any wobble caused by an uncentered needle. After several adjustments the needle becomes well centered and I cut the girdle faces to their finished size. At that point, I can just cut and polish the step-style pavilion as usual. I used 42, 45, and 48 degrees for the pavilion face angles. I cut the culet faces deep enough to remove the tiny stray needle we saw earlier. Now, it is ready to transfer: After transferring the stone, I cut the crown as usual using 46, 41 and 26 degrees for the crown angles. The next photo shows the crown prepolished and ready for the table to be cut. Notice that the needle is right in the center of the stone: Two views of the finished stone still on the dop: Finally, two views of the finished stone show the single needle - and the needle reflected in each face of the gem. Diamonds: Modern Diamond CuttingDiamond Cutting BackgroundOne of the hardest substances on earth, only a diamond is hard enough to cut other diamonds, although it can be easily cleaved or fractured due to its defined cleavage planes. Like wood, diamond has a "grain," and the rough stone must be cut with the grain, rather than against it. Diamond cutting can be traced back to the late Middle Ages. Prior to this time, diamonds were used in their natural octahedral state. The first improvements on nature's design involved a polishing of the crystal faces, which was called the "Point Cut." As further refinement progressed, one half of the crystal would be cut off, creating the "Table Cut." At the time, diamonds were valued primarily for their luster and hardness. Table Cut diamonds appeared black to the eye. The Modern Round Brilliant cut (below) is the culmination of several hundred years of experimentation and development. Cutting a Rough DiamondCutting a raw diamond into a faceted and polished gem-quality stone is a multi-step process. Each step is critical to the final outcome. The steps are:
Marking: A rough stone is marked prior to cleaving or sawing to determine the direction of the grain and cleavage, eliminate waste, and bypass any inclusions or imperfections. The natural shape of the rough stone will also be a major factor in deciding how to cut the stone. An octahedron can be cut into one or two Round Brilliants but a square Princess cut will result in the least amount of waste due to the square shape of the stone. Asymmetrical crystals such as macles are used primarily for fancy cuts. Cubic shapes are ideal for a square Princess or Radiant cut. High-tech computerized helium and oxygen analyzers are now used to evaluate a stone prior to cutting. Cleaving: Cleaving refers to splitting a stone along its grain by striking it. A rough stone is cleaved if there are conspicuous defects and/or inclusions which would prevent it from being made into a single gemstone. Cleavage is the tendency of crystalline materials to split along defined cleavage plane. Due to its atomic structure, a diamond can be cleaved in four directions parallel to each of the four octahedron crystal faces. Cleaving is a critical step as a mistake by the "cleaver" could fracture, or shatter the stone. Sawing: A stone-cutting saw is a thin disk made of phosphor bronze. As the saw blade rotates it continues to pickup or "recharge" itself with diamond dust which is the cutting agent. It can take several hours for the saw blade to cut through a 1k rough diamond. Bruting: The rough is placed in a chuck on a lathe. While the rough stone rotates on thediamond lathe, a second diamond mounted on a dop is pressed against it, rounding the rough diamond into a conical shape. This step is also referred to as "rounding." Faceting: To facet a round brilliant, the "blocker" or "lapper" will cut the first 18 main facets, then a "brillianteer" will cut and polish the remaining 40 facets. The cutting (also called "placing") and polishing of each facet is accomplished by attaching the stone to a dop stick with cement, then pressing it against a revolving cast iron disk, on a scaife, or lap that has been "charged" with diamond dust. During this faceting stage the angles of each facet must be cut to an exacting standard in order to yield maximum brilliancy, and maintain symmetry. Fancy Gem Cuts: Glyptic & Fantasy Cuts (Fantasieschliffe)Fancy CutsWhen a cutter selects a particular gemstone cut there is usually a practical reason for the decision (yield, color zoning, rough gem shape, etc.), although sometimes it is simply a preference for style. Additionally, each gem variety lends itself to certain types of gem cuts based on its durability, color, and crystalline structure. In diamonds, asymmetrical rough crystals such as macles are usually unsuitable for symmetrical cuts such as the modern round brilliant, and lend themselves to a "fancy cut" style. These fancy gem cuts can follow the best attributes of the rough stone while eliminating or avoiding cleavage planes, internal flaws, and inclusions. Popular fancy diamond cuts include the "Baguette" (bread loaf), "Marquise" or "Navette" (little boat), "Princess Cut" aka Square Brilliant Cut, "Heart", "Briolette" (a form of Rose cut), Pear (teardrop), and the Trillion which is triangular in shape. For bicolored gemstones that have distinct color transitions such as tourmaline or ametrine it may be beneficial to utilize an elongated fancy cut such as an emerald, baguette, navette, or fantasy cut. Concave FacetingConcave gem faceting cuts are a relatively new trend on the gem-cutting scene (amethyst - above, left). Invented by Doug Hoffman in the early 1990s, the technique was perfected by American gem-cutter Richard Homer. The unique conical-shaped faceting creates a high amount of brilliance by refracting and dispersing more incident light than a conventional gem facet cut. Cross Cuts, French Cuts, & Step CutsAn emerald cut, as shown in the diagram at the top of the page (upper, left), is a modified step cut with the corners cut at a diagonal angle. With a step-cut, the crown, pavilion, and the table are all cut in rectangular facets. This type of step-cut does not produce much brilliance, but it is an effective cut for showcasing a stone's color attributes (as with emeralds). Popular variations of the step-cut are the Scissor-Cut or Cross-Cut, Baguette Cut, and theFrench-Cut (above, center). These cuts add slightly more brilliance to the stone a dark stone, and are good for concealing internal flaws. The french cut is also used on very small stones where a brilliant cut would not be practical. Navette CutThe "navette-cut" or marquise cut (shown in simplified form - above, center) is a popular choice for colored stones such as topaz, citrine, amethyst, and aquamarine. The navette cut may have been the creation of King Louis XV of France, who was so taken with the delicate shape of his courtesan's (Marchioness Madame de Pompadour, below, right) mouth that he commissioned his court jeweler to create a gem cut in its likeness. Composit Gemstone CutsComposit gemstones are created by bonding two or more materials together to form one gemstone. When the final gem is made of two different materials it is called a "doublet," and when made with three, a "triplet." Common doublet or triplet gemstones are emerald andOpal, usually combined with quartz or glass. Compositing is used to improve color and add durability. In faceted composite stones, the crown would be the natural material. So far, the consistent theme in all of these fancy cuts is their symmetry. As a fancy gem cut takes on a more asymmetrical shape, such as the Isosceles Triangle Cut citrine above (left, with trillion diamond), it would be labled as a "fantasy cut." Fantasy Cuts (Fantasieschliffe)There is also a new addition to the gem cutting universe: the "fantasy cut" or fantasieschliffe. There is probably no person who is more famous at this relatively new art form than the German stone cutter Bernd Munsteiner. The Munsteiner family (Bernd, Tom and Jutta) at Atelier Munsteiner have been pushing the boundaries of stone cutting to their limits with their endlessly imaginative shapes and forms. A somewhat softer, more organic variation of the Munsteiner family's Fantasieschliffe cuts are the "Glyptic Illusions" sculptured gemstones cut from Bart Curren. Bart, also known for his digital photography of gemstones, lives and works in Washington State, USA. Although modern saws, grinders and polishers are used to create these fantasy cuts, this type of stone cutting brings back the lost art of "hand-cut" craftsmanship. Although the only limit to the design is the cutter's imagination, an intimate knowledge of a mineral's cleavage and optical or refractive properties in necessary to get the most out of a stone's natural beauty. Gem Cutting Technology: Lapidary Equipment & TechniquesCutting a Rough Gem StoneCutting a raw stone into a faceted and polished gemstone is a multi-step process. Each step is critical to the final outcome. The steps are:
Marking: A rough stone is marked prior to cleaving or sawing to determine the direction of the grain or "cleavage", eliminate waste, and bypass inclusions or imperfections. The natural shape of the rough stone will also be a major factor in deciding how to cut the stone. Cleaving: The term "cleaving" refers to splitting a stone along its grain by striking it. A rough stone is cleaved if there are conspicuous defects and/or inclusions which would prevent it from being made into a single gemstone. Sawing: The rough stone is cut to a shape that approximates the shape of the finished cut stone but without the facets. Girdling: The rough is placed in a chuck on a lathe. While the rough stone rotates on the lathe, a second diamond mounted on a dop is pressed against it, rounding the rough diamond into a conical shape. This step is also referred to as rounding or bruting. Faceting: The cutting and polishing of each facet is accomplished by attaching the stone to a dop stick and pressing it against a revolving lap (see "Facetron" below). During this faceting stage the angles of each facet must be cut in order to maintain symmetry and produce maximum brilliance. Brillianteering: In diamond cutting, if the primary faceting or "cross-working" is done by a separate craftsman, the final 40 facets of a round brilliant cut diamond's 58 facets will be cut by a Brillianteer. Gemstone Color EvaluationWhen cutting certain types of gemstones that have peculiarities with their color such as zoning(sapphire, tanzanite, etc.) or color shifts (ametrine, tourmaline, etc.), it is critical to determine the best orientation of the cut within the rough gem. For evaluating the color of a gemstone, it is crucial that the identical light source, intensity, and color temperature is used every time. A "Gem Light Box" gives off a stable 4800 to 5200 Kelvin degrees (natural, indirect sunlight). Some light boxes have a UV component to the light for grading pearls or colored stones (Fraunhofer Solar Spectrum Chart, below). Faceting Design & Rough EvaluationDiamond Manufacturing factories use sophisticated electronic equipment for cutting and evaluating cut diamonds. Using the latest hardware and software to create highly accurate 3D models, these scanners measure the angle of inclination of a facet and its azimuth, allowing the operator to pre-visualize a 3D model of the cut stone. HeliumPolish Scanners are used for Round Brilliant Cuts as well as Fancy cuts. A device called a Pacor Oxygen Scanner can be used for optimizing rough stones based on purity to evaluate inclusion removal or reorientation. Diamond BrutingGirdling or bruting the rough is a critical phase where the stone is placed on a lathe while a second diamond mounted on a dop is pressed against it, rounding the rough diamond into a conical shape. AutoBruters use the latest technology to preform "non-contact" measuring to overcome inherent problems in the rounding process. using live video and image analyzing software, potential out-of-roundness and any deviations from the desired dimensions and a computer will guide the machine to take necessary actions by slowing the bruting speed or pressure. Gem AnalyzersAn "IdealScope" or "H&A Viewer" (below, center) uses a 10x lens with a pink/red reflector positioned in front of the diamond under a central viewing hole, allowing the viewer to see how much of the red/pink light refracts back from the diamond. The resulting pattern will be a good indicator of faceting proportion and symmetry. For performing Cut Analysis on a finished stone, a Dia-Analyser (above, right) uses a camera to take photographs of the finished diamond while it is being rotated. The computer's software will digitize and the analyze the data to quantify all of the cut parameters. Lapidary & Gem Cutting EquipmentThe machine to the upper left (Poly-Metric Scintillator 88 Digital) and to the upper right (Facetron) are semi-automated faceting machines. Machines such as these have taken some the guess-work out of stone cutting, but a skilled craftsman must cut a rough stone to its optimal size and and take ito account any inclusions or imperfections that must be eliminated in the cutting process. By examining the rough stone under a microscope or jeweler's loupe, the gem-cutter will decide which type of cut will show the stone's best color attributes, and what (if any) inclusions to avoid. Facetron & Lapidary Gem SawThe Facitron (left) and Scintillator (upper right) are water-cooled faceting machines designed to make cuts at precise angles by mathematically plotting out to depth and degree of a given facet. The rough gemstone is held by a chuck called a "dop" "dop stick" or "dop chuck" and ground against a grinding plate called a "lap". The rough stone is held to the dop with hot-wax glue. By adjusting a dial indicator (protractor) the gem-cutter can control the degree of cutting angle to a tolerance measured in hundredths of an inch. The image above (bottom, center) shows a rough gemstone attached to a dop stick. The image to the right (above) is a combination lapidary gemstone saw (slab saw) and grinder. Cabochon GrinderIf the material to be cut and polished is translucent to totally opaque (agate, onyx, malachite, etc.) a cabochon cut will most likely be employed. Gem-Cutting and Lapidary InfoPrettyRock, Step-by-Step Gem Cutting Gemstone Artists, The Gem Cutting Process Faceting Machines, Faceting How-To Tips Rock Hounds, Faceting By Hand Gem Society, Fundamentals of Lapidary Faceting US Faceters Guild, Faceting Diagrams & Gemstone Designs Bowers Museum, The Art and Nature of Precious Stones Folds, Reflection & Refraction of Light in a Diamond AGL, Measuring Color Via Spectrophotometer Diamond Cut, HCA IdealScope Folds, Diamond Design - by Marcel Tolkowsky Diamonds: Patented Signature Diamond CutsNotable Patented & Proprietary Diamond CutsSince the early 1900s there has been a proliferation of elaborate diamond cuts that have been developed by master gem cutters, mathematicians, scientists, and entrepreneurs - each trying to improve on the tried-and-true Old European cuts, and their modest brilliance and light return. Every conceivable cutting theory is tried, (more facets, less facets, etc.) and when suitably scrutinized by the gem trade, it is put in front of the ultimate arbiter of quality - the consumer. Some have gone on to become household names such as the Asscher cut, or the widely marketed Leo cut which is a modified round-brilliant sold by Leo Schachter Diamonds; but some like the Barion Cut have disappeared into obscurity. Here is a collection of just a few of the many "signature" diamond cuts that have been produced over the last 100 years. Asscher Cut The Asscher Cut was developed by Abraham and Joseph Asscher of the Royal Asscher Diamond Company of Amsterdam in 1902. Popular in Art Deco jewelry of the period, the Asscher diamond cut has a squarish octagonal shape with a step cut, cut corners and a small table. The cut has a deep pavilion and a high crown, and the culet is square. The Asscher brothers cut the famous 3,106 carat Cullinan Diamond into eleven gem stones, with the two largest stones, the Cullinan 1 and Cullinan 2 being set into the crown and sceptre of the British Crown Jewels. Barion Cut The Barion square cut (aka Barion square cushion cut) was invented by Basil Watermeyer of South Africa in 1971, and was the forerunner to the princess cut. The name "Barion" or "Barion cut" was never trademarked, and its patent has expired. The Barion square cut diamond has a 4-fold mirror-image symmetry, and a total of 81 facets, not including the 16 girdle facets. Barocut The Barocut® diamond cut is a patented, modified rectangular (baguette) cut that was developed by Baroka Creations, Inc. of New York in 2000. The Barocut is also called a "two heart diamond" due to the illusion of two mirrored hearts meeting at the culet. A Barocut diamond has a total of 77 facets, or to increase light-dispersion, 81 facets on the cut corner (cushion) version. Barocut stones are also sold in tapered shapes. Barocut diamonds are promoted and sold exclusively through the Baroka Creations catalog, or the company website. The Barocut is available in sizes from 20 points to 3 carats, and in all diamond colors and/or clarity grades. Context Cut The Context Cut is a square cut that was developed by Dr. Ulrich Freiesleben of Germany in the early 1980s then patented and trademarked in 1997. The Context Cut consists of two back-to-back pyramids (an octahedron), forming a square shape when viewed from the top. The Context Cut follows a rough diamond crystal's natural octahedral shape, with star-shaped cross facets cut diagonally into the pavilion. The cut has a total of 8 facets plus a girdle. The Context Cut design was based on an earlier patented design by Bernd Munsteiner from the early 1960s. The cutting process requires a high-quality rough, and creates a high amount of waste, adding up to 50% to the cost when compared to a Round Brilliant cut diamond. The Context Cut is used to cut colored gemstones by Julius Petsch of Idar-Oberstein, Germany. Eternal Cut The Eternal Cut diamond was designed and patented by master Israeli diamond cutter, Gabi Tolkowsky, nephew to the inventor of the Modern Round Brilliant cut, Marce Tolkowsky. It is sold exclusively through the 270 year old firm of Garrard & Company in London. In 1998, Garrard & Co. merged with the jewelry firm Asprey, to become Asprey & Garrard, parting ways in 2002 to again become Garrard. The Eternal Cut has a total of 81 facets, 23 more than a modern Round Brilliant cut, creating a unique 'flower petal' pattern surrounding the cutlet, and a 'softer' briliance than a traditional round brilliant cut. The Eternal Cut is being sold exclusively at Garrard's main London store and Harvey Nichols stores in Great Britain. Flanders Brilliant Cut The Flanders Brilliant Cut (aka Fire Brilliant) is a modified Radiant or Princess cut with truncated corners that form an octagon with brilliant faceting. The Flanders Brilliant has 33 crown facets and 28 pavilion facets for a total of 61 facets. The Flanders Fire-Brilliant was developed by Flanders Cut International of Antwerp in 1983, and the cut was named after the Flanders region of Belgium (Antwerp) where the cut was first preformed in 1987. The cut is distributed by the National Diamond Syndicate (NDS) of Chicago. Flower Cut The 'Flower Cut' series was created by Gabi Tolkowsky in 1986, who was commissioned by De Beers to create new cuts as a way of marketing unusual, off-color stones. The Flower Cut is actually a series of five fancy cut shapes: the Dahlia, Fire-Rose, Marigold, Sunflower and Zinnia cut. The Flower Cuts employ unconventional cutting angles and dimensions, designed to maximize the brilliance and color of diamonds while increasing their yield. The Flower Cuts were never patented or trademarked by De Beers in order to increase their popularity and use. The Dahlia is a 12 sided oval shape with 63 facets. The Fire-Rose is a hexagonal shape designed to produce higher yields. The Marigold is an octagon shape with 73 facets, that is suited to a relatively flat rough. The Sunflower has 43 facets in unusual, angular shapes. The Zinnia is a round fancy shape with 73 facets, 48 of which are clustered around the culet to increase fire. The Gabrielle Diamond The Gabrielle® Cut is a modified brilliant cut (triple brilliant cut) that was created by DeBeers desinger/consultant Gabriel Tolkowsky in 2000. Unveiled at the Las Vegas Gem Show in 2001, the Gabrielle has a total of 105 facets, which is 47 more than a traditional 'Tolkowsky' round brilliant cut, adding greater brilliance and fire than standard brilliant cuts. Other than the traditional round brilliant shape, the Gabrielle Cut is available in carre, emerald, heart, marquise, oval, and pear shapes. Leo Cut The Leo® Diamond, (aka Leo Schachter Diamond), is a patented symmetrical round cut created by Leo Schachter Diamonds, LLC. The Leo diamond cut has a total of 66 facets, 8 more facets than the Round Brilliant cut's 58, maximizing the amount of light returned back as scintillation. The Leo diamond cut is the first to be certified for fire and brilliance as measured by a 'BrillianceScope,' and each diamond comes with a "Return of Light Certificate." The Leo Diamond is marketed through the Kay Jeweler chain. Lucida Cut The Lucida (TM) Cut is a patented diamond cut that was created by Tiffany & Company in 1999. The Lucida diamond cut is a modified square or rectangular (Marquise) cut with truncated corners, a high-step crown (similar to the Asscher Cut), small table, brilliant-style faceted pavilion (similar to a Cushion Cut), and a total of has 50 facets. The Lucida is sold exclusively through Tiffany's retail chain. The Lucida diamond cut is marketed as a wedding cut, sold in solitaire engagement/wedding bands, eternity bands, and three-stone rings. Quadrillion Cut The Quadrillion® Cut (aka Squarillion Cut) is a modified square princess cut that was developed by Israel Itzkowitz and Betzalel Ambar in the late 1970s, and was patented and trademarked by Bez Ambar Jewelers of Los Angeles in 1980. Prior to the Quadrillion, square shaped diamonds were step-cut limiting their brilliance. The Quadrillion was the result of three years of optical research to create a square diamond cut that can claim a similar brilliance to a round diamond. There are a total of 49 facets. Radiant Cut The Radiant Cut is a modified emerald cut shape that was developed, patented and trademarked by Henry Grossbard of the Radiant Cut Diamond Company (RCDC) in 1977. It was the first emerald shaped diamond cut to have brilliance and fire similar to that of a round brilliant diamond. Upon the expiration of the patent, the Radiant Cut became a fully accepted diamond shape in the jewelry business. RCDC launched the 'Original Radiant Cut' diamond brand In 2002, and all Original Radiant Cut diamonds weigh at least 0.70 carats and come with a GIA Certificate and an "Original Radiant Cut Diamond Certificate" guarantying that the stone meets the ideal proportions as designed by Henry Grossbard. There are 25 crown facets and 36 pavilion facets for a total of 61 facets (not including 8 girdle facets). The pavilion is similar to a Barion cut, and the table is a bowed out rectangle. Starburst Cut The Starburst Cut was patented and trademarked by the Louis Glick Diamond Corp. of New York in 1978. The Starburst cut was created to bring out the highest amount of color to fancy yellow diamonds. The crown of the Starburst Cut is similar to that of the radiant cut, but the pavilion is completely different. There are 49 crown facets and 40 pavilion facets, for a total of 89 kite and star shaped facets. The Starburst cut is especially suitable for a octahedral rough, with weight losses in the fifty percent range. The starburst faceting pattern is designed to focus color near the top of a stone, making the hue of fancy yellow diamonds more intense. Starburst Cuts are mounted and sold directly through Cartier, Harry Winston, Nieman Marcus and Tiffany. Trilliant Cut The Trilliant Cut (aka Trielle, Trillian, Trillion) is a triangular cut designed and trademarked by the Henry Meyer Diamond Company of New York in 1962. The Trilliant trademark has since lapsed, and the Trilliant is now a generic term for a triangular brilliant cut. The Trilliant has the Schoenflies point group symmetry of a round brilliant, reworked into the shape of a trillion (triangle). The Trilliant Cut has a total of 31 facets. The pavilion has two differently sized sets triangular facets with a large triangular table. There are two variations of this cut: the Curved cut used for solitary stones, and Uncurved cut used for accent stones. The Trilliant cut gives a high brilliance, fire, and scintillation when cut to the correct proportions. Diamonds: Ideal Cut - Modern Round Brilliant DiamondIdeal Cut vs Standard Cut DiamondArticle Copyright © 2009 AllAboutGemstones.com When deciding how to cut a rough diamond, a cutter must make a cost-benefit analysis as to how to maximize the cut stone's value. An octehedral rough diamond will yield two round brilliant cut stones (see diagram below). The objective is always to maximize carat weight, but in order to do this, compromises would have to be made. The clarity of the stone, and the amount of internal inclusions will play an important part in the decisions as to how to maximize yield. This is accomplished by reconciling three key factors - weight retention, cut proportions, elimination of any inclusions. Reconciling Cut & Weight RetentionIf the rough stone has a colorless D through F rating and has very few inclusions, it would be cost effective to sacrifice some carat weight in order to finish with two "Ideal" cuts. If, on the other hand, the rough stone has some coloration and/or is heavily included, it may be better to aim for a higher carat weight utilizing a "Standard" cut.
When dealing with a near-perfect (or flawless) stone the cut that is generally preferred is the classic "round brilliant" cut. This is primarily due to the fact that this cut has yet to be improved on for two reasons: 1. it is the most efficient cut for maximizing yield, and 2. it is the best cut for showcasing a high-quality stone's fire and brilliance. This is why it is very rare to see flawless stones cut into fancy cuts such as emeralds, hearts, etc. The Modern Round Brilliant CutThe modern "Round Brilliant Cut" (below) was developed by Belgian diamond-cutter Marcel Tolkowsky in 1919. This cut is also known as the "Tolkowsky Cut" and "Tolkowsky Brilliant." Even with modern techniques, the cutting and polishing of a diamonds resulted in a loss of as much as 50% of the stone's total weight. The round brilliant cut was a partial solution to this problem. The round brilliant cut is beneficial when the crystal is an octahedron, as two stones could be cut from one crystal. In the diagram of a "Round Cut" diamond (above and below), you will see that there are 8 "star" facets, 8 "kite" facets, 16 "upper girdle" facets, 16 "lower girdle" facets, 8 "pavilion" facets, 1 "culet" facet on the bottom, and one "table" facet on the top of the stone for a total of 58 facets. An "Ideal Cut", "Premium Cut" or "Modern Round Brilliant" (Tolkowsky Round Brilliant) diamond as shown in the diagrams above would have the following basic proportions according to the AGS:
In the 1970s, Bruce Harding developed new mathematical models for gem design. Since then, several groups have used computer models and specialized scopes to design new diamond cuts. Tolkowsky, Eppler & Scan D.N.Variations on the Tolkowsky Brilliant (diagram below) are the "Eppler" (European Practical Fine Cut, or Feinschliff der Praxis) with a table width of 56%, crown height of 14.4%, and overall height of 57.7%. The "Scan D.N." (Scandinavian standard, or Scandinavian Diamond Nomenclature) diamond cut has a table width of 57.5%, crown height of 14.6% and overall height of 57.7%. Other variations of the MRB include the "Ideal Brilliant", invented in 1929, the "Parker Brilliant" invented in 1951, and the "Eulitz Brilliant" invented in 1972. To quantify a diamond's cut quality, gem labs will use a variety of equipment such as a BrilliantScope, H&A Viewer, Ideal Scope, Sarin Diamension and/or FireTrace. AGS Triple Ideal or 'Triple 0' GradeThe AGSL grades a diamond's cut quality using three parameters: Polish, Symmetry, and Proportions. Each parameter is given a 'grade' from 0 (Ideal) to 10 (Poor). When all three parameters are in perfect harmony the diamond is given a "Triple 0" or "Triple Ideal" grading. The AGSL grades a diamond's symmetry and proportions according to where facets intersect, and crown/pavilion angles, but does not measure or quantify relative facet angles and/or individual facet ratios. A perfect blending of facet symmetry, facet ratios, and facet angles will yield a perfect 'Hearts & Arrows' Diamond pattern when viewed through a H&A Viewer. As with all human endeavors, there is a constant attempt to 'build a better mousetrap;' and there has been numerous attempts to improve on this tried-and-true formula with the introduction of new signature diamond cuts that claim to have a higher light return, more brilliance and fire, etc.. Producers split hairs over cut angle, cut proportions, and number of facets, but at the end of the day it may simply come down to consumer preference and/or marketing. One thing is for sure - like Einstein's theory of relativity, Tolkowsky came up with a "brilliant" idea almost 90 years ago, and it still survives in some form today. |
การเจียระไน (Cutting)
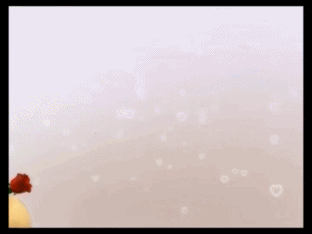